|
Post by Beekster on Apr 26, 2020 17:57:55 GMT -6
If you stay in this hobby long enough, you will eventually find yourself in situations where you want to have duplicates of kit parts, sometimes many of them. The solution is to cast copies in polyurethane resin, and it isn't really all that hard to do. While there are lots of choices for the chemistry, the basics are these: RTV (Room Temperature Vulcanizing) rubber, and two-part polyurethane resin. The box below is a starter kit from Alumilite, and can be found at most hobby shops for around thirty bucks:  Let's see what's inside the box:  At the back, left to right, we see two bottles with the components for the resin, a small tub of RTV, and a bottle with the chemical hardener for the rubber. In the foreground, two popsickle sticks are included to mix the rubber with, a blue cube of clay, two cups to mix rubber and resin in, and underneath it all the instructions. But this isn't quite everything you need...  This stuff comes in handy, too: A large lump of modeling clay, various sizes of Lego bricks, and pipettes with which to draw the resin components out of their bottles and mix them evenly. These are disposable, and can be had by the thousand for cheap from laboratory supply stores. You can just read the instructions at the bottom of the second image above, and right there it tells you to make a mold box. That will be the subject of the next installment, along with tips on making your master patterns.
|
|
|
Post by JCON on Apr 26, 2020 18:40:36 GMT -6
This should be fun!!!
|
|
|
Post by dogfish7 (R.I.P.) on Apr 26, 2020 19:52:16 GMT -6
Cool beans! You're reading my mind. 
|
|
|
Post by BUCKY on Apr 26, 2020 21:01:40 GMT -6
I'm in for this! Us car builders rob kits, too, especially if trying to restore an old gluebomb!
|
|
|
Post by Beekster on Apr 27, 2020 15:58:38 GMT -6
What you see here are two mold boxes, made up of Lego bricks with modeling clay carefully squished into place to form a top surface for the mold, and a place for the part to sit. The mold on the right is upside down, to illustrate how the clay needs to be tight against the Lego bricks to get a good seal when the RTV is poured  Once you have a mold box ready you can add parts by squishing them into the clay. But to cast parts, they have to be properly prepared like these Sherman transmission pieces:  The white styrene you see are the sprues through which the resin will pour. The sprue is partially embedded into the clay so that the piece stands up and RTV can surround it to make the mold. Note that some pieces have .005" styrene glued to their back sides; this is to ensure that resin has a path to flow all the way to the end of the parts and provide an escape route for air bubbles. More on that later when we get to actually making castings. The transmission shift lever in back has more plastic built up on the side to stiffen it, otherwise the casting would break when you try to remove it from the mold. In this case, it still might; this is an experimental effort to do this part in a single-piece mold rather than a two-piece mold. All the parts you see here will be done in single-piece molds, where the RTV surrounds the part and the finished casting is removed by flexing the mold and slowly prying the piece out. If I have problems, I will revert to two-piece molds but I won't go into more detail on that until later.   This shows what the two largest pieces look like in their mold boxes, nearly ready for casting. The front wall of the transmission base is removed to show how it sits in the clay. These two pieces are otherwise ready to have RTV mixed and poured!
|
|
DPNM
GAINING SPEED

Posts: 561
Likes: 1,270
|
Post by DPNM on Apr 27, 2020 18:22:59 GMT -6
This is a good tutorial. Thank you for posting it. I've done some of my own casting but there is always a lot to learn by seeing how others do it.
|
|
|
Post by Beekster on Apr 27, 2020 18:31:27 GMT -6
This is a good tutorial. Thank you for posting it. I've done some of my own casting but there is always a lot to learn by seeing how others do it. Happy to help! I haven't done castings in a while, but my methods haven't changed from what I did before. But I've finally run out of stockpiled parts to do interiors for Sherman-family tanks, so it's time to make some more. My source for these pieces is the Academy M10 kit, and their M36 has a couple of other useful items. I understand that Rye Field has done a new M4A3E8 Sherman with an interior, so I'll have to pick one of those up and crib more pieces from that.
|
|
DPNM
GAINING SPEED

Posts: 561
Likes: 1,270
|
Post by DPNM on Apr 27, 2020 19:06:13 GMT -6
I just got a kit that is missing a front wheel/steering part. I traded with someone else for the same kit but I haven't gotten it yet. I plan to cast any parts I need so I can then make two cars.
I've only done one single piece mold. The ones I usually make are simple two piece molds. I do mine a bit different. That's why I'm following along here. If I can learn a better way, great.
|
|
|
Post by JED on Apr 27, 2020 23:46:18 GMT -6
Very interesting, I'm watching for sure
|
|
|
Post by Beekster on Apr 28, 2020 15:26:44 GMT -6
Stay tuned, everyone...I've mixed and poured some RTV. Thing is, this basic kit would have you dump the entire itty bitty amount of hardener into the RTV, mixing it all in one go. The mix ratio is listed as 10:1 silicone to hardener by weight, but this stuff is liquid so that doesn't work. In the past, I've generally done that ratio by liquid volume, say 30ml of RTV to about 3ml of hardener. That's what I did here, more or less. We'll see if it set up...if not, very bad. Odds are it will cure but how long that takes is not precisely known. The instructions say 8 to 18 hours for the RTV to cure hard enough to de-mold the master parts, which is a pretty wide margin. In the past, I've always waited about 24 hours to be sure. Assuming that the hardener ratio is close, it ought to just be a matter of time for it to cure completely (and I have had molds take a few days to fully set up).
No pictures of this step because it's pretty messy when you are working with it and I don't want to get anything on my nice lightbox. Mix and pour is pretty straightforward. Air will get into the RTV during mixing, and air will be forced out of nooks and crannies around the master pattern(s) as the RTV flows into the mold. It's a good idea to tap the mold vigorously on the table for a couple of minutes to help shake out any air bubbles. We don't want those forming around the master, since that will create a cavity that fills with resin and mars the final casting.
|
|
|
Post by dogfish7 (R.I.P.) on Apr 28, 2020 16:43:24 GMT -6
Pour on Beekster. 
|
|
|
Post by Beekster on Apr 29, 2020 9:25:04 GMT -6
OK, this is promising and has somewhat assuaged my fears about curing. When I tapped at the molds this morning, this one was least sticky, so I disassembled the box holding it together. It held it's shape, which is of course what we need to see...it has at least cured enough to do that. I removed the clay, and worked the master free and it came out clean. That too, is good. I can still smell the silicone, though, which means it is still curing. No casting today, and I will leave the other two molds for several more hours before taking apart those boxes and de-molding the masters just to be on the safe side.  In the background you see a pile of silicone goop. That is most of the remains of what was in the mixing cup, plus the stuff that leaked through gaps in the Lego bricks. Making mold boxes out of Lego bricks is fast and easy, but they aren't completely liquid-tight so you lose some of the RTV you pour. But not really! You see, RTV will stick to itself quite nicely, so I will keep this stuff. For the next molds I make, I will stuff this material down into corners before I pour fresh RTV. This material will be fully integrated into the next mold, and whatever leaks from that one will be kept for the next one and so on. The only thing to be careful of is to keep this old stuff away from the master pattern itself, since it won't flow and conform to the contours of your part. In fact, if you have old, worn-out molds of the same type of RTV, you can cut them up into pieces and add them to new molds to reduce the amount of fresh RTV that must be mixed to make your new mold. In my case, I have some old molds but I'm not sure about the chemistry since I've used more than one brand over the years.
|
|
|
Post by Beekster on Apr 29, 2020 14:03:10 GMT -6
And here are the other two molds from this first batch. I pulled the boxes apart and de-molded the masters after about 24 hours, but I won't pour resin for another day or so...they could still use more cure time, if the sniff test is anything to judge by. Once again, the parts pulled cleanly. This RTV is really flexible, so I have some concerns about warping of the big transmission piece when I pour resin. The solution is easy; just build a Lego box around it once again so it can't distort as the resin cures. So far, so good... 
|
|
|
Post by dogfish7 (R.I.P.) on Apr 29, 2020 16:06:51 GMT -6
Cool!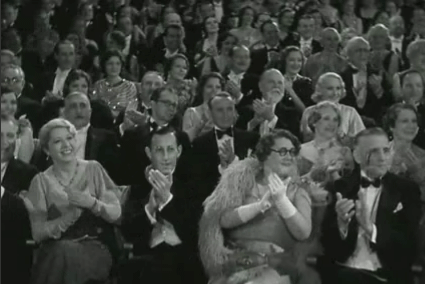
|
|
|
Post by JED on Apr 30, 2020 12:58:49 GMT -6
Looking pretty good
|
|
|
Post by Beekster on Apr 30, 2020 16:33:29 GMT -6
First pours are done; partial success...I've got to re-learn some things.  The big transmission piece came out OK, but has some holes & bubbles. Likewise, some of the parts on the gang mold didn't cast completely because I didn't get all the air out. And it turns out a two-piece mold will be better for the rounded transmission piece, since you can see the mold split getting it out. So, what went wrong here? 1. Trying to do too much at once. I mixed too much resin, and had to get it into molds while I still had working time...and with this resin, that's only two minutes. Use less, do one or maybe two molds, and just use up the droppers instead. 2. As a result of #1, didn't spend enough time working the molds to get all the air out. If only one is poured, there's more working time. 3. I cast the molds bare. Dusting a little baby powder in the mold will probably help, since it helps draw the resin into nooks and crannies. I've got enough RTV left in this set to mix up another couple of molds, I think, but there are more to be made like a two-piece for that transmission part and some of the control rods, which are too slender to survive trying to pull them out of a vertical mold. So I will have to order more RTV and hardener, but a pound of RTV is $27 plus shipping versus 3 ounces in this starter set. Edit: More RTV is on the way for $35 including shipping, so I can keep playing with this. Just poured a mold for a driver's compartment floor, which is a big one...about an inch tall, two inches wide, and half an inch thick. Lots more bits to make molds for, but until the additional RTV arrives I am limited to probably one more, and I'm always limited by my Lego supply. When the malls reopen, I think I'll take a trip and get some more. They have bins, and you can buy random stuff in bulk...perfect for uses like this.
|
|
|
Post by Beekster on May 1, 2020 10:31:47 GMT -6
OK, this morning's iteration is a bit better:  I did these in two separate batches about fifteen minutes apart. The gang mold was done first, followed by the transmission. The latter came out very nicely indeed, as did most of the parts in the gang mold. Slowing down, powdering the molds, and spending time working out air bubbles really helped the quality. I still have issues with the foot pedals not wanting to cast, so I need to take apart the gang master and work out another solution for the pedals. They might wind up done as part of a larger two-piece mold. A piece broke off the gang mold during the de-mold process this morning, so I need to rearrange how I do those things anyway. All these parts were left in the mold for considerably longer before pulling them out, and in truth the gang mold could have stayed in longer...it was still a little pliable, though I flattened it out again. Though the product says de-mold time is about ten minutes, there's no harm in leaving the mold alone for an hour or more. More time equals harder resin. The leftovers which stay in the cup are a good indicator of how the resin is curing. It may be only ten or fifteen minutes for it to change color from translucent brown as mixed to cream as it hardens, but it will still be flexible...especially the film that sticks to the sides of the cup. Go ahead and pry it out, and play with it if you wish. But wait until that film wants to crack & break when you manipulate it to think about pulling your castings from the mold. If the film has gone brittle, the resin is solidly cured.
|
|
|
Post by JCON on May 1, 2020 10:46:11 GMT -6
Looks good to me!!!
|
|
|
Post by JED on May 1, 2020 13:36:37 GMT -6
Good result
|
|
|
Post by Beekster on May 1, 2020 14:41:36 GMT -6
And this is the eventual direction for this stuff:  These particular castings have some flaws and may not actually be used on this project, but this mock-up shows roughly how they are supposed to fit in there.
|
|