|
Post by ARMORGUY on Apr 8, 2021 12:04:35 GMT -6
You're putting a lot of effort in it and it shows. Keep building fella !
|
|
|
Post by JCON on Apr 8, 2021 16:02:53 GMT -6
Excellent madness my friend!!!
|
|
|
Post by dogfish7 (R.I.P.) on Apr 9, 2021 9:29:17 GMT -6
Beekster is a Perfectionist. 
|
|
|
Post by Beekster on Apr 9, 2021 10:54:52 GMT -6
Beekster is a Perfectionist.  One of my most prominent flaws!
|
|
|
Post by JCON on Apr 9, 2021 12:00:07 GMT -6
Beekster is a Perfectionist.  One of my most prominent flaws! One of??? 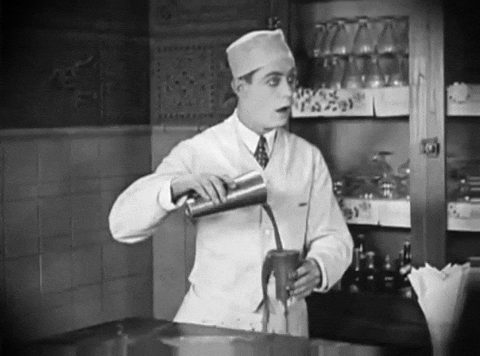
|
|
|
Post by dogfish7 (R.I.P.) on Apr 9, 2021 15:06:20 GMT -6
Yep! 
|
|
|
Post by Beekster on Apr 10, 2021 12:59:22 GMT -6
Having set aside the first yarder for a day or so following this morning's unfortunate events, I began looking at tracks for the other one. I have not had a response yet from the equipment dealer, but the track shoes look like pretty simple construction so I started working things out conceptually. So, I've got the suspension bits and rollers mocked up again on one side:  Looks to me like each bolt head corresponds to the front of one link in the drive chain, and each link is a little less than a quarter of an inch long. Stands to reason that a single track pad is attached to each link, yes? If so, that's 36 links per side. Might be feasible to just build all 72 rather than cast them, but we'll see. Now we come to scale issues. The rubber band track measures out at about 626.75mm or .705" wide, or 24.675" wide. That is way wrong. The standard track width is 800mm or 31 inches per the brochure and yes, I am aware that 800mm really works out to 31.4" wide. An optional track is 700mm or 27.56" wide. This is what it looks like with a link of each size fitted to the roller:  Yep, no clearance for the larger shoe at proper scale. In addition to working out a decent shape for the links, I will also have to make them a bit less than the scale 31" wide. There's not much side to side motion on the track in operation, particularly at five miles an hour or less, but there has to be some clearance. It just occurred to me that I can probably shim everything out. I can punch discs out of .020" and .030" sheet and drill holes for the axle stubs more or less on center. The shim would never bee seen so really accurate location won't matter. I'll see what that looks like.
|
|
|
Post by dogfish7 (R.I.P.) on Apr 10, 2021 13:54:47 GMT -6
|
|
|
Post by Beekster on Apr 10, 2021 16:12:35 GMT -6
Good thing I went down this road of considering building my own tracks. My first clue was that the track to hull side gap was bigger on one side than the other as I worked with the shims. Hmmmm... Either my center post wasn't quite centered or the die cast track frame isn't as symmetrical as one would expect in a plastic kit. It took a lot of grinding of the post so that the track frame would move around more, and popping off the side plates that fit in the middle of the frame. Now I can get the gaps side to side even within about ten thousandths (rather than the right side gap being about .080" wider than the left). That's the good news. The bad news is that without a tight fit to the center post like before, working on other stuff is going to be harder. I was hoping to avoid permanently fixing the track frame in place with epoxy for as long as possible, but I might not have that luxury. The frame was locating too far to the left side, which contributed to the track pad problem there...and that is the side shown in all the images above. I still think I will need the shims in there, but they are just tacked in with superglue so popping them off, if necessary, won't be too hard. These shots were taken after the shims went on, but before I figured out my side-to-side location error.   At least now I can be certain that I won't have to deviate from scale width for the track pads, which will make the contrast with the Sherman version all the more apparent.
|
|
|
Post by JCON on Apr 10, 2021 16:50:04 GMT -6
Nice planning saves problems later for sure!!!
|
|
|
Post by Beekster on Apr 10, 2021 18:40:48 GMT -6
Nice planning saves problems later for sure!!! Indeed. Further tinkering has me convinced that the track frame isn't quite square and true, but I am loathe to do too much with pliers and hammer to tweak the ends with the wheel axles too much. Don't dare break anything; I will have to ensure that there's considerable slop in the wheels instead to get them to line up. The solution to centering the frame is also simple: Shims of styrene strip to make the gaps even.
|
|
|
Post by ARMORGUY on Apr 11, 2021 13:24:11 GMT -6
Nothing wrong with being a perfectionist fella, as long as you keep enjoying yourself. Impressive work!
|
|
|
Post by Beekster on Apr 11, 2021 14:29:53 GMT -6
|
|
|
Post by dogfish7 (R.I.P.) on Apr 11, 2021 14:47:32 GMT -6
Those are some really nice reference shots. 
|
|
|
Post by JCON on Apr 11, 2021 14:58:48 GMT -6
Very useful indeed!!!
|
|
|
Post by Beekster on Apr 11, 2021 16:08:33 GMT -6
The second iteration of the track shoes looks promising, even unfinished:   This, however, does not:   I am rather at a loss about what to do about this. While the chain drive parts have some flex, the inside ones are simply significantly taller than the outer ones, so the track shoes sit at an angle. The wheels too are rather too large; the track shoes will ride up over them and not be in contact with the drive chains.  This shows clearly the vertical problems. This is what I get for using something that is not much more than a toy on which to base a serious model. Could I make fairly accurate track shoes with integral chain drive bits, and through holes for track pins? Yeah, I suppose. But I had better be dead on with measurements, which I don't have. And then I would have to figure out what to do for the sprocket and other structure. I'm not a CAD guy, so it's not like I could draw these up and then spend a fortune having parts 3D printed. The front rollers aren't a huge hurdle; new ones of smaller diameter could be fabricated. Or if I have an appropriate piece of brass rod for an axle I could tack these on with superglue and turn them smaller. But that vertical difference is a serious problem. The rubber band track put some tension on these parts so the difference wasn't as apparent, though the bowing of the rubber track hinted at it. Much thinking to do here...
|
|
|
Post by JCON on Apr 11, 2021 16:19:37 GMT -6
Hummm that is interesting.... can you lower the top back section by sanding or filing it down without messing with the integrity of the part?
|
|
|
Post by Beekster on Apr 11, 2021 16:41:13 GMT -6
Hummm that is interesting.... can you lower the top back section by sanding or filing it down without messing with the integrity of the part? Perhaps I can. The parts are also quite solid at front and back where the chain drive detail rides over the backing plate. By getting in there with a razor saw, I can remove material which ought to allow the top run to flex downward, which is what I need. Another option is to take a file to the track frame, and grind down the solid supports on the inside of the top support rollers that are cast in. That too would allow the chain part to flex downward. Yet another possibility, if I get close with some combination of the methods above, is to superglue some thin Evergreen stock to the outer parts with the sprockets, to slightly raise the profile of the chain run on top. Still thinking...
|
|
|
Post by dogfish7 (R.I.P.) on Apr 11, 2021 17:10:28 GMT -6
It might be easier to add shims, to raise it slightly above the drive wheels.
|
|
|
Post by JCON on Apr 11, 2021 17:22:32 GMT -6
Long as there is enough flex in the track to go over it...
|
|